Dr. Tao was employed by AGRI-TECH, Inc (FMC Corp) from 1991-1996. From 1993-1996 he served as the Vice President/Director of R&D for the prominent manufacturer of complete lines of fruit and vegetable inspection and packing equipment designed to efficiently and effectively bring food products to the market.
While at AGRI-TECH, Inc., Dr. Tao developed the Merlin vision sorting system (ASAE AE50 award for the outstanding technology) for 100% inspection of a wide variety of fruit & vegetables including apples, peaches, pears, tomatoes, and citrus. It sorts fruits into 8 simultaneous quality grades at a speed up to 44 tons/hour. It is widely installed in the United States, Canada, and other countries, and dramatically improved fruit packing efficiency and quality -- with huge labor savings and high-skill job creations (sorting over 45% of total U.S. apples alone in each year for the past decade).
After the fruit has gone through the cleaning, coating, and drying process, it is carried to a sorting area for the inspection. Along the sorting conveyer, workers inspect each fruit, remove defective fruit or unwanted items, and redirect different grades of fruit as required. Commonly, a roller conveyer is used to rotate the fruit for overall surface inspection. At this stage workers perform sorting operations that machines are not capable of doing.
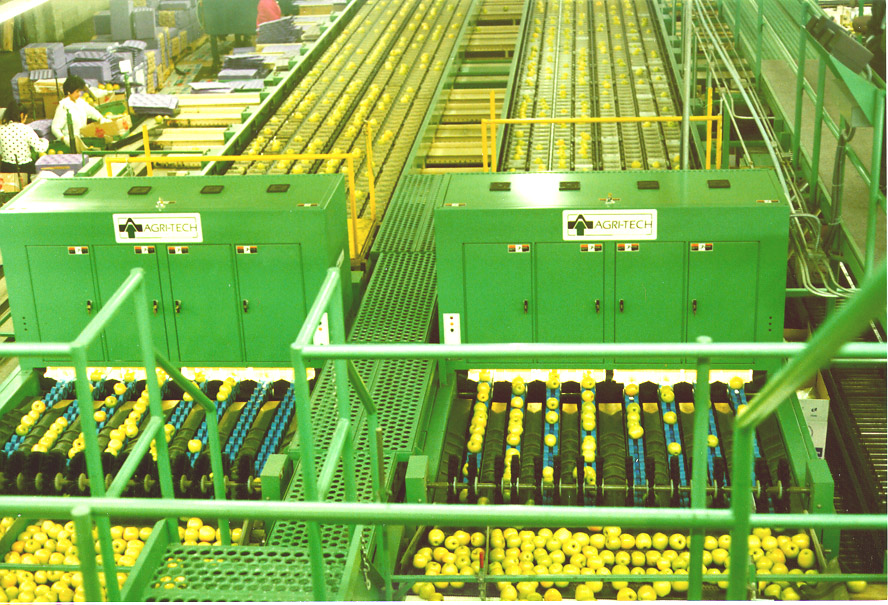
In large packinghouse operations, sorting machines using machine vision are installed to sort fruit into different grades based on weight, dimensional size, color, shape, limited defects, and other parameters. A typical machine vision fruit sorting system [1] is shown in Fig. 4. On the roller conveyers, fruit are singulated into pockets so they can be handled individually. Usually the fruit is rotated on rollers while passing through a vision chamber. Inside the chamber, video cameras take one or more images of each fruit. Linked to each camera, a computer embedded with a digital image processor instantly processes the images. This information is combined with information from other sensors, in many cases weight, and each individual fruit is assigned a grade based on this information compared against the sorting parameters specified by the operator. A typical user control console of a vision system is shown below. Research and development in non-destructive inspection and automated sorting according to quality factors such as internal and external defects, acidity, soluble solids, firmness, and other parameters are still continued efforts in the scientific and engineering community [2-34].
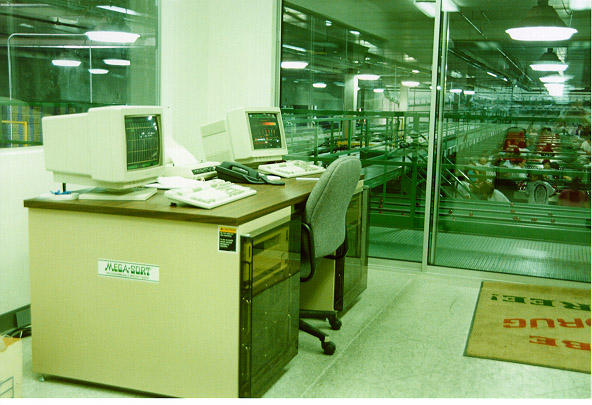
After grading the fruit is transported by a mechanical sorting machine that discharges the fruit at many different locations along it’s length. The “drop” location for each individual fruit is determined by the operator based on it’s assigned grade and where in the packinghouse it is to be packed. When a fruit reaches it’s assigned location it is removed from the sorting machine by some methods. Generally the fruit is carried in a pocket or holder which can hinge down backwards, hinge down to the side, or tilt up to cause the fruit fall out. In some cases an ejector is used to knock the fruit out. It then falls onto a conveyer which carries the fruit to its packing location. The mechanisms for releasing are carefully engineered to minimize damage to the fruit. Typically, soft pads, brushes, and/or ramps are also used to reduce the impact of fruit to each other and to the collection conveyer. The computer controlled sorting machines give the packinghouse the flexibility to sort fruit to meet many different customer requirements. Large apple packing lines sometimes have the capability of separating fruit into 64 or more classes.
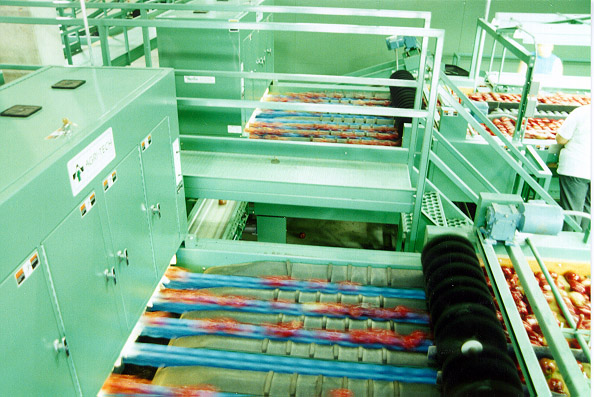
|